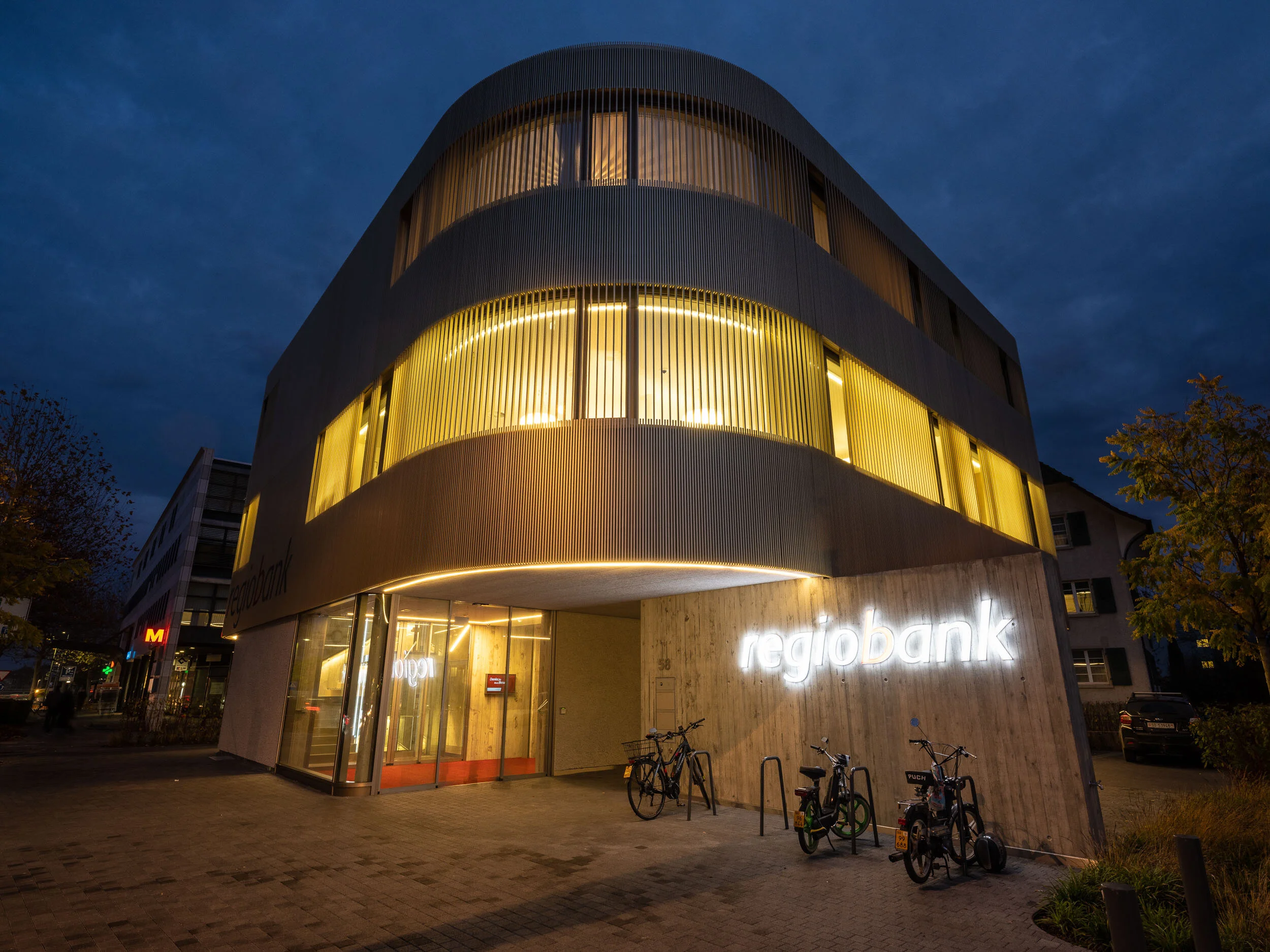
The Challenge
To efficiently realise golden anodised slats with a trapezoidal cross-section, closely spaced and partly running over the windows, on a building with round corners - this is not an everyday task.
The substructure should also be designed with as few thermal bridges as possible and with minimal material costs.
The Ecolite Solution
Thermo H-brackets with double slits are used for a horizontally continuous, very rigid U-profile. This maximises the bracket spacing and minimises heat loss, and also makes it easier to round the symmetrical U-profile for the corner areas.
The slats were prepared in our workshop as ready-to-install gratings with individual numbers and only had to be fixed to the U-profiles on site with four to six self-tapping screws and according to our execution planning.
Ecolite Products
These Ecolite products were used:
Special Thermo H-brackets, blank U-profiles and lacquered Z-profiles (partly rounded in different radii), object-specific slats with profile connectors made of extruded profile and milled covers for the profile ends.
Picture gallery
For an enlarged view just click on the corresponding picture
Photos: 720.ch
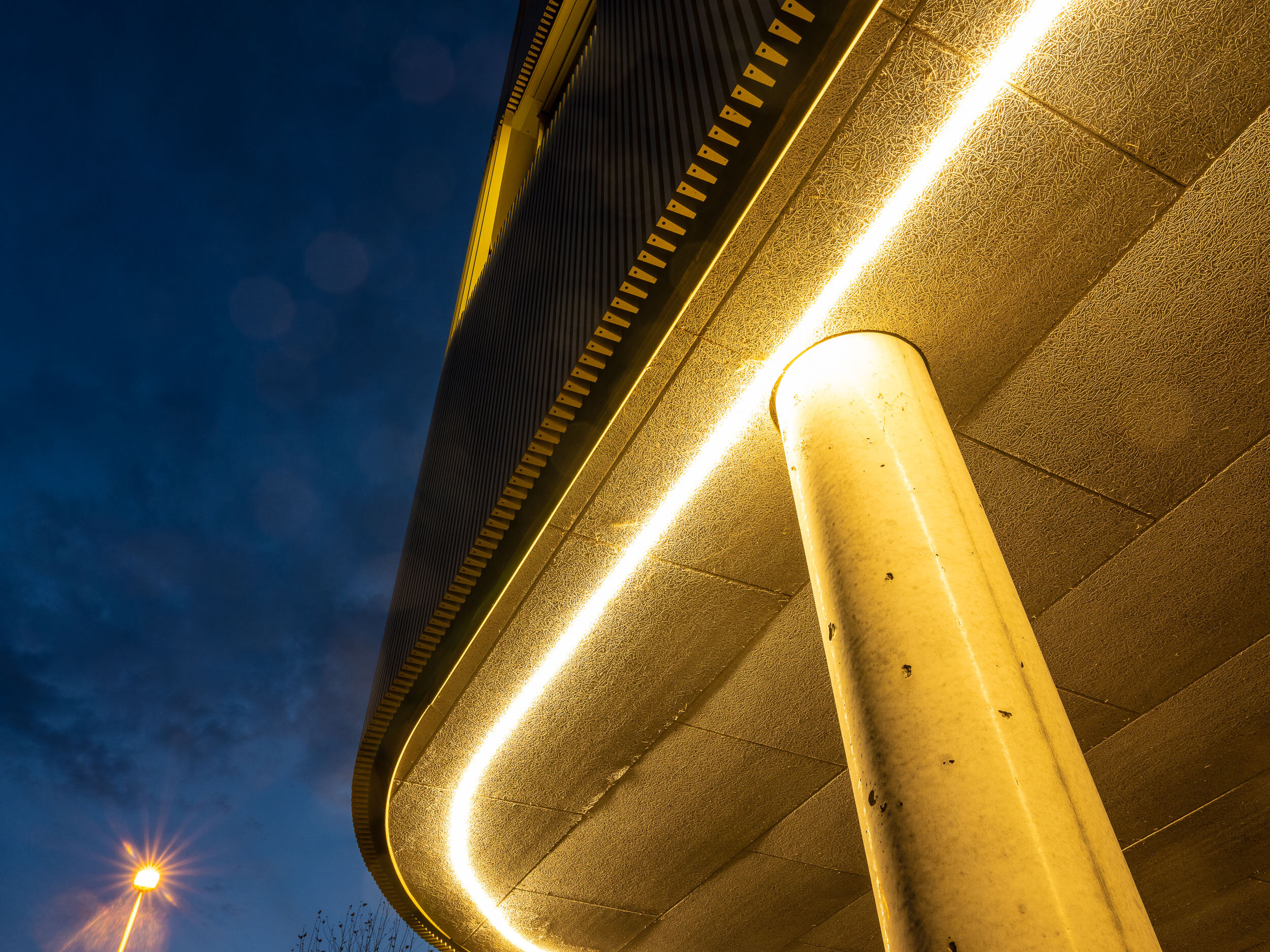
Designed and built with great care
The Regiobank Zuchwil is an attractive gem with a harmonious façade that runs like a ribbon without interruption and even partially across the windows. The two upper floors hover above the ground floor, which is set back, in exposed concrete and glass.
The façade itself consists of fine, vertical, gold-coloured anodised aluminium profiles with a trapezoidal cross-section. The narrower profile side is directed towards the building. The individual slats are riveted in a tight grid to horizontal, black-painted Z-profiles. Under the wind seal, special Thermo H-brackets with double slits are embedded in the insulation to accommodate a horizontal U-profile. From a thermal and installation point of view, this solution is perfect, as brackets the required strength could be achieved with an absolute minimum.
Challenges in construction
The challenge was clearly, on the one hand, to dilate the façade without cracking noise and without compromising the visual appearance and, on the other hand, to find a practicable way of attaching the thin louvres, some of which were over four metres long, to the façade behind the scaffolding efficiently and without causing damage.
Another sticking point was the round building corners with different radii. In the end, all visible sides of the stacks should always have the same distance to each other. To prevent the fine slats from sounding like organ pipes in the wind, and also for aesthetic reasons, thousands of milled, anodised covers were installed.
Well prepared is important
In the production rooms of Ecolite AG, our employees, under the supervision of Samuel and René Bregenzer and according to plans by Roger Mingard, drilled and riveted individual, ready-to-install and shear-resistant façade gratings of approx. 80 cm width in templates specially made for this purpose. The numbered grating elements could then be screwed directly onto the horizontal U-profiles at the construction site using a special bit between the slats. A horizontal, optically closed dilatation joint was also introduced in the middle of the building. Anodised profile connectors fixed into the lamellas on one side ensure that the stakes of the upper elements match those of the lower elements completely and that the individual lamellas are fixed again at their ends.
The packaging and transport of the partly bulky but at the same time rather delicate elements presented us with another challenge. Thanks to the temporary storage on the roof of the building, however, this problem was alleviated. There, the elements were protected from outside interference and could be led from the roof directly behind the scaffolding. In the end, crane truck driver Peter Tanner delivered all the elements to Zuchwil in one piece and the assembly team did their part to make the project a success.